March 1, 2022 / By admin
The dry tumbling process: Grinding
From the theory to the practice: becoming Master in Polishing
As anticipated in our previous newsletter, the information sheets regarding the dry tumbling process intend to offer a detailed description of the single process stage.
Today we will talk about the first stage of the dry tumbling process: Grinding.
First of all it’s extremely important to describe the dry tumbling process
What is the dry tumbling process?
The dry tumbling is an industrial process used to remove surface defects generated by previous processing. The main goal of this process is to achieve a qualitatively perfect, shiny and brilliant surface.
Achieving a perfect, shiny and brilliant surface is the main goal of the Dry Tumbling process.
It’s important to introduce here, the “flat” surface concept. A flat surface is free of scratches, marks and is very smooth.
Why is it so important to introduce the concept of “flat surface”? Because a flat surface will appear more shiny to the human eye.
It’s all a matter of reflection: a ruined, matt surface (full of scratches) will reflect the light differently than a flat, smooth surface.
Surface with defects Flat surface – without defects
How can I understand if a surface is flat?
The parameter for measuring imperfections on the surfece is the Roughness. The instrument for measuring surface roughness is called the Rugosimeter (a kind of turntable, which records surface irregularities).
The next parameter is called Gloss Unit. The instrument for measuring the level of gloss of a surface is called Glossmeter– it measures the grade of reflection of light on the surface. Higher the value, more shiny will appear.
So how do you get a flat and shiny surface through the tumbling process?
The tumbling process and the surface quality are based upon a mechanical friction generated from the rubbing of the media on the components to be tumbled.
This may sound complicated: inside the barrel the media, covered with abrasive paste, will hit the surface, this will polish the surface. Take a closer look at the tumbling process in this article.
The most significant process parameters are:
- Shape, material and weight of the media.
- A rough and heavy media will hit the surface differently than a light and less edgy media.
- The abrasive compound provided as paste, liquid or powder.
- A media covered with an heavy cutting compound will hit the surface differently than the same media covered with a less cutting compound (for example a compound for the Shining step).
Discover Pai Cristal surface treatment media:
Pai Cristal has been developing and producing abrasive pastes and tumbling media for various materials since 1965.
Discover Pai Cristal abrasive pastes for the process of tumbling cellulose acetate and injected plastic:
Grinding
The first stage is called Grinding.
The targets of the grinding stage are essentially three:
- To remove the surface defects generated by the mechanical processing.
- To get the same surface level either on the mechanical processed areas as well on the non-processed areas
- To get round the sharp edges of the rough components.
What happens to the surface during the Grinding stage?
The main goals of the grinding stage are to remove surface defects generated by mechanical processing, to get the same surface level and to get rounded shapes. The second stage of the Dry Tumbling process is called Smoothing – we’ll take a closer look in the next article.
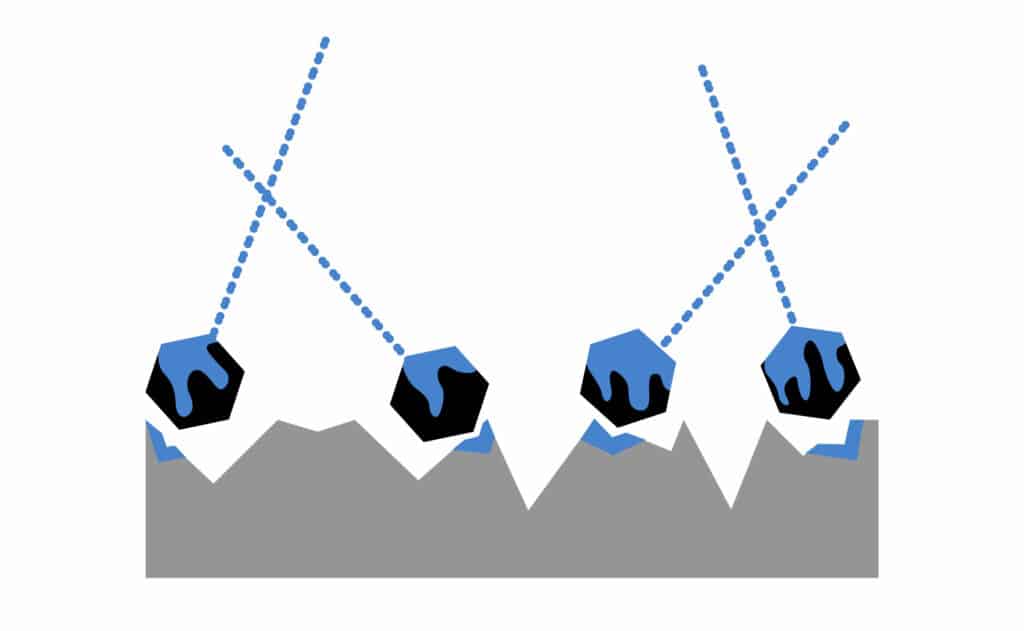
During the Grinding process will be used media that enable to generate a stronger action; for that reason, the media applied for this stage are heavier and bigger wood media (normally 7 mm rhombus or bigger) or plastic rhombus.
In the informative images, a macro view of what happens to the surface during the grinding stage.
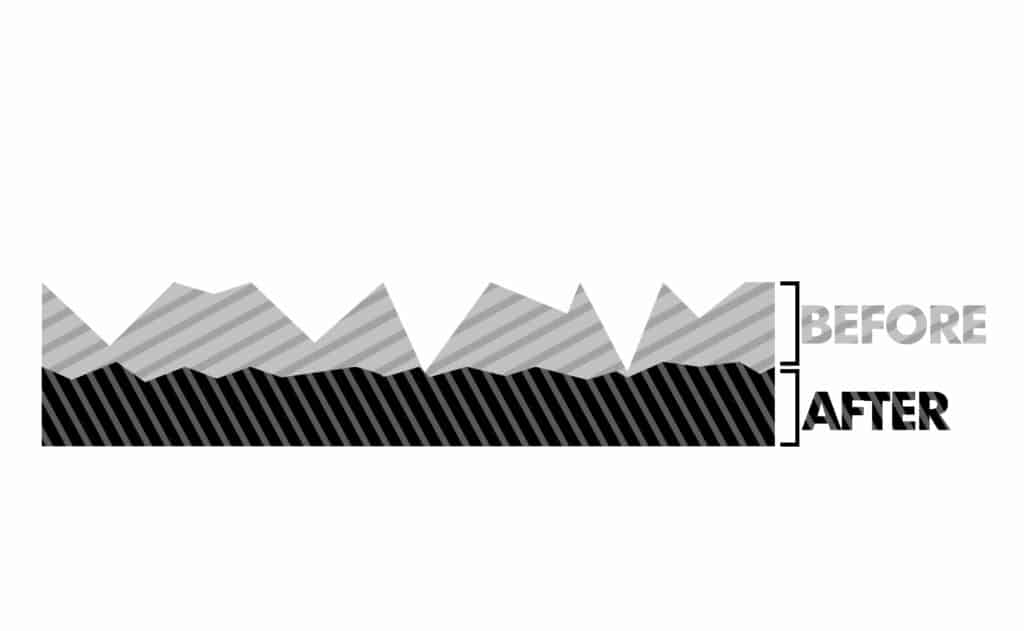
To fully understand how relevant is the mechanical abrasion produced by the media and compound. Below are highlighted the Roughness (Ra) values measured on a test panel before and after the Grinding stage:
Values before and after Grinding stage:
- Ra 1,335 µm (measure taken on a milled-process)
- Ra 0,3 µm
Grinding is, therefore, the first step in the tumbling polishing process and it is very important to proceed to the next steps and finally get a flat, shiny and brilliant surface.
In the next “from theory to practice: Master in Polishing” article we will analyze the second tumbling stage: the Smoothing.
Pai Cristal, since 1965 offers complete solutions for dry and wet tumbling. In addition to abrasive compounds and media, also technical advice and rotary tumblers:
Stay up to date: download the tumbling processes of each material, fill out the form!
Do you need an advice for the polishing stage or a process to tret a specific material? Contact us!